I was given an amazing tour of the Mirror Laboratory at the University of Arizona today. What a place!!! It totally amazed me, and I don’t amaze all that easy with technology.
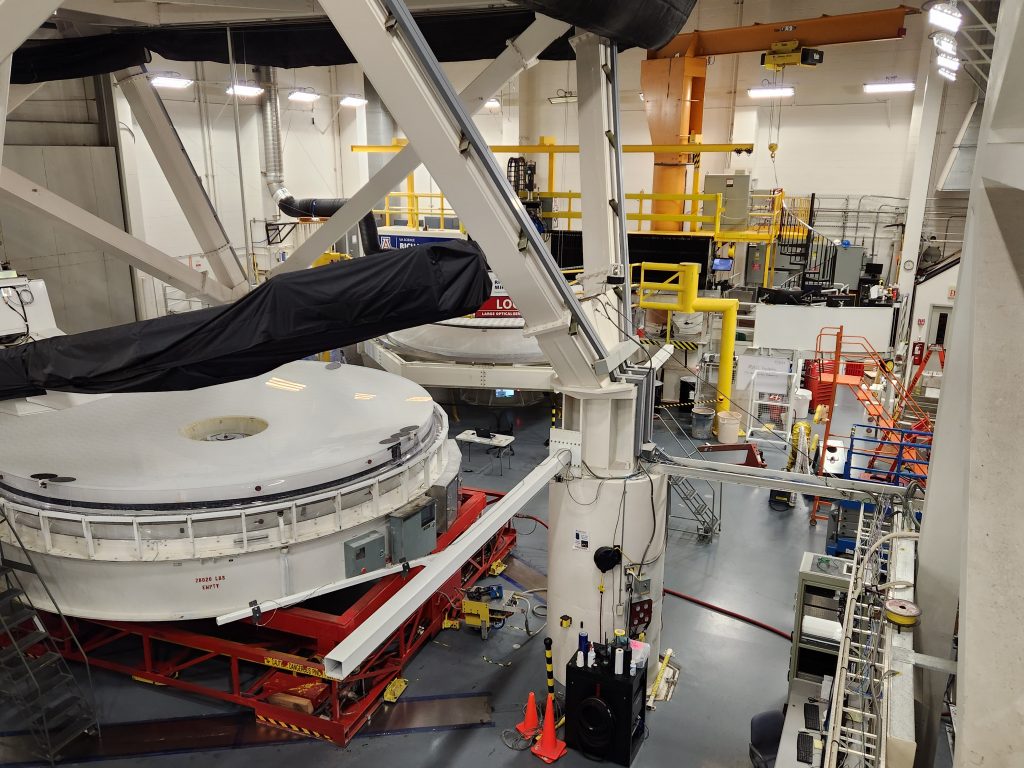
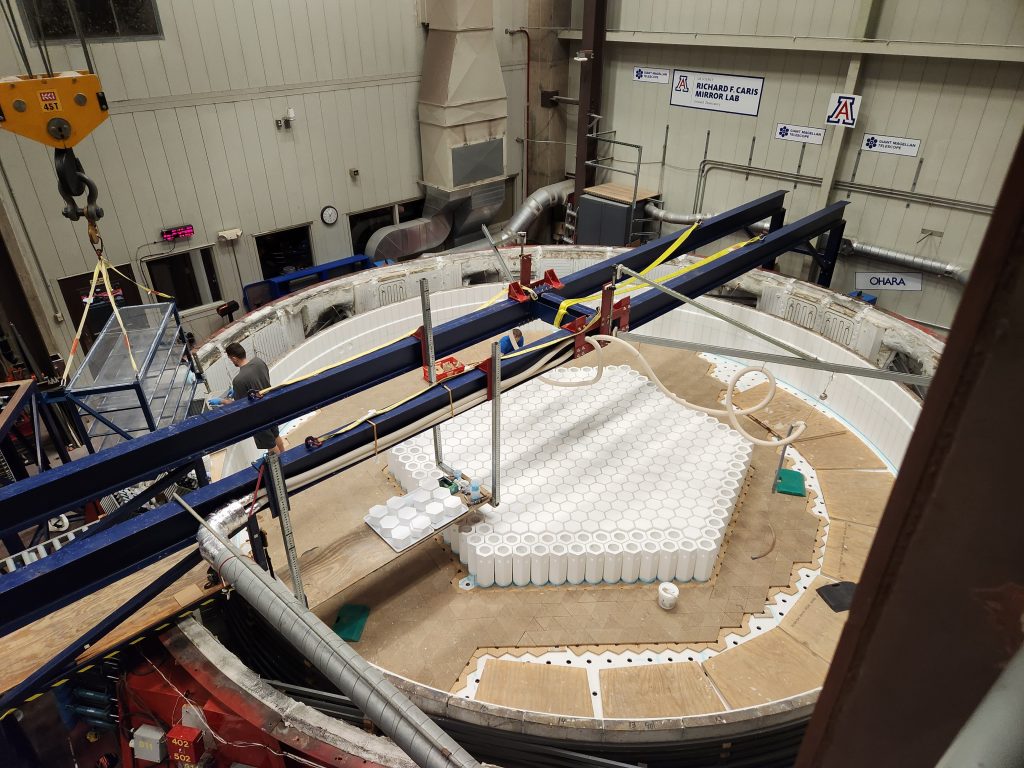
It is a bit to get an idea of scale in these photos. You can see the guy working in the photo to the right. The photo on the right shows them preparing the mold getting ready for casting. This step should be done sometime around September. The mirror on the left is a “small” mirror being tested for shape. You can’t quite see them, but there are three more much larger ones in storage in the background. The one on the right is for the Giant Magellan Telescope. That telescope will have 7 of these gigantic mirrors mounted on a single mount, just like a “regular” telescope. The mirror shown is the last of the set. The others have been cast and are in storage. The glass takes five years to get, so you kind of have to plan ahead a bit.
I don’t have the time or space to go into the details here, you can Google it if you are interested in the future telescope, or this mirror lab. This is the one place in the world where this sized mirror can be made. The mirrors are mostly hollow so aren’t nearly as heavy as would be the case without the process used here. It casting process is a bit complex, but basically the white structures being placed in the right hand photo are the places that DON’T get glass, there is a small space between these that get filled with the glass, resulting in a honey comb once they wash the white stuff out. There is also a layer of glass on the bottom and another on the top. The top pieces forms the parabolic shape of the mirror. To cast it, fist sized chunks of glass are arranged on top of the white things, which are different lengths to approximate the final shape of the surface. The glass is melted while the whole thing spins. Some of the glass runs down between the white forms, and some stays on top to create the mirror surface. The spinning makes the glass form the desired bowl shape. Once it has finished melting and filling in the spaces, it is slowly (weeks) cooled. Then it has to be polished and finished.
The process for making these relatively light weight, huge, mirrors started around 1980 when the inventor took a couple of wife’s pyrex dishes, broke them into pieces, and melted them to see if they would form a single, optically pure piece of glass. It worked, and over the period of more than a decade or so they came up with this process of spin forming hollow mirrors.