Yesterday was the beginning of “spring cleaning” in my shop. My approach to working in my shop leaves much to be desired from many points of view. One of my really “bad” habits is that I tend to not put things away as I work on projects. Things just get left out on the surfaces for easy access, but after awhile they pile up to the point where I no longer can find them when needed. When that happens it is once again time to put things back where they “live.” Of course that means that the old adage of “a place for everything and everything in its place” becomes important – but unfortunately it is not the situation in my shop. There are places for many things, but there is always a great deal of “overflow” having no home. This stuff just keeps floating around on the surface – always in the way and looking messy.
My wife and I live on a five acre piece of land that could be a “mini-farm”, but is really just a huge back yard. Bigger than we can, or want, to maintain. Our solution to this is to hire part time folks to help out with the “yard” work. This arrangement helps us and gives them a flexible job. However, when it rains we make up jobs that aren’t really necessary so they can work out of the rain – but keep some work going their way. Often this extra work has to do with “cleaning up,” which is where my problem with not have a place for everything comes up.
In an effort to make things look nice and neat, these folks have a tendency to put that loose stuff that is floating around into five gallon buckets – all jumbled indiscriminately together! I end up with buckets of unknown stuff hidden in the corners of the shop. This makes things look nice, but of course it also means that I have no idea where any of it is, leading to great frustration when I need something. As disorganized the situation appeared before, at least I could find things. The approach of filling buckets is just the opposite.
I decided that part of the problem is that don’t have any way to provide enough “homes” for all of the little odds and ends. I have some really nice plastic bins that hang on a wall, but not enough of them. They look like this
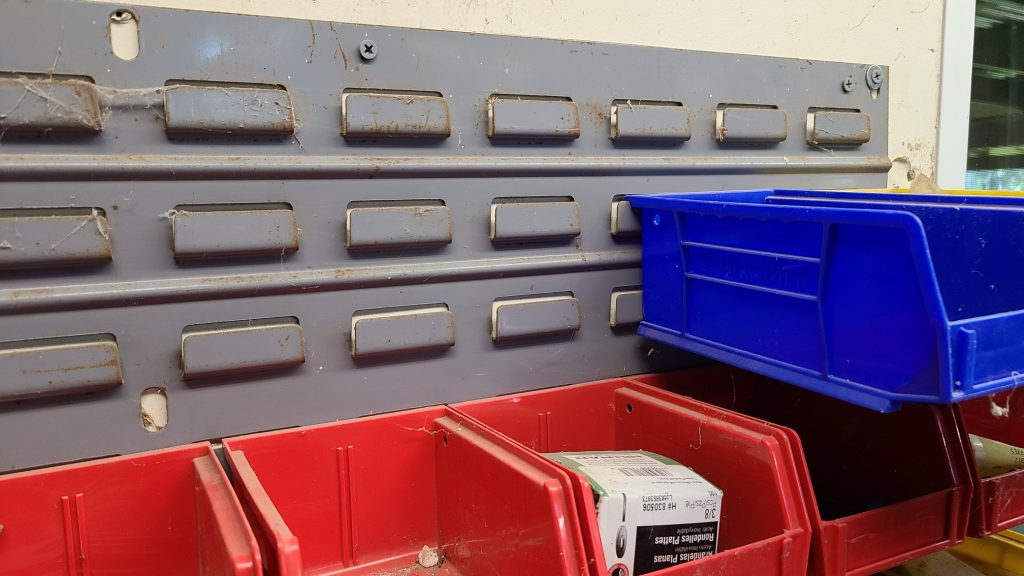
These are great, but there are no nearly enough of them. There are more hanger spaces than I have bins, so a partial solution to my problem of not enough “homes” is to purchase more bins. Unfortunately, the local hardware stores don’t stock the same brand of bins. They all stock other brands that make almost identical bins. These other brands make bins that are the same colors, same thickness, apparently the same molds with different brand names. As far as I can tell, these other brands are “knock offs” of the original ones that I purchased decades ago. I took a sample to the hardware store to do side-by-side comparisons and they seemed identical in every way, so I purchased a bunch of them.
I was all set and ready to start “organizing” when I got home, but found that the new bins wouldn’t quite fit the tabs on the wall rack. I could get them on by using two hands and quite a bit of force, but they didn’t just slide right on like the original ones. Upon careful inspection I found that they weren’t “exactly” the same. The original ones have tiny ridges in the tab that hooks onto the rack. Like this:
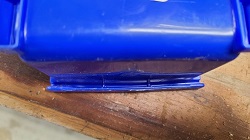
Those two little “bumps” in the middle keep the opening large, and straight, enough to fit onto the wall unit. That little detail wasn’t included in the “re-engineering” of the knock-offs. This little detail, this little oversight, transformed a cleaver “borrowing” of a design from a quality item to an item that doesn’t work.
I am writing this as an example of the kinds of things that separate quality products from so-so ones. It is the reason that I often pay a little more for something that appears to be “the same.” Tiny differences can change the experience of using the product from being easy and comfortable, to difficult and frustrating. Sometimes the differences are as blatantly obvious as the lack of the tiny tabs, sometimes it is hidden in the properties of the materials – perhaps the difference is just a short cut on the heat treatment of the metal being used. Often the “short cut” doesn’t even change the cost of production, as in the case of the bins where the presence of the tiny bumps would have cost nothing – but the understanding of the features of the higher quality product was not recognized. “Quality” is the sum total of all the “little things.” Mass production aimed at continually achieving ever smaller savings results in the continued spirally down of many products and many production techniques – worldwide. In most cases these cost improvement don’t translate into cheaper products for the consumer, they only translate into higher profits and lower quality products.
Enough of my evangelizing about the apparent slow slide into meritocracy. I just wanted to share what I thought was an interesting case of an “almost” (but not quite) successful clone of a successful product. The outcome was that I returned the bins to the local store and instead purchased them online from Amazon. I try to make as many purchases as possible locally, even when the costs are a bit higher and I have drive 40 miles to get to town (20 miles each way) to get them. But I am finding that harder and harder to do because the selections at the local stores are rapidly shrinking, but also because the quality of merchandise offered is steadily going below my personal cutoff for “acceptable.” I avoid buying inexpensive (meaning low quality) tools and equipment because it is just too expensive due to “not quite” working, with frustrations instead of joy in its use, and the much shorter life before it breaks and has to be replaced.